Due to our constant pursuit of enhancing our system, we began reevaluating hoses and flows within the brewing system. The design of the previous servo-pinch valves had dictated the placement of the valves and consequently the routing of all hoses within the system. Unfortunately, the valve placements often necessitated unnecessarily long hoses. During the optimization of hose lengths, we realized that there were significantly smarter hose routes available, but this would mean deviating from the previous valve arrangement.
We came to the conclusion that it was time to replace the servo valves with something new while simultaneously upgrading the hoses to larger dimensions. After some research on sanitary pinch valves, we designed the valves below, which are based on small pneumatic cylinders. The parts are 3D printed using Formlabs Rigid 10K resin, a glass fiber-reinforced engineering resin known for its exceptional strength.
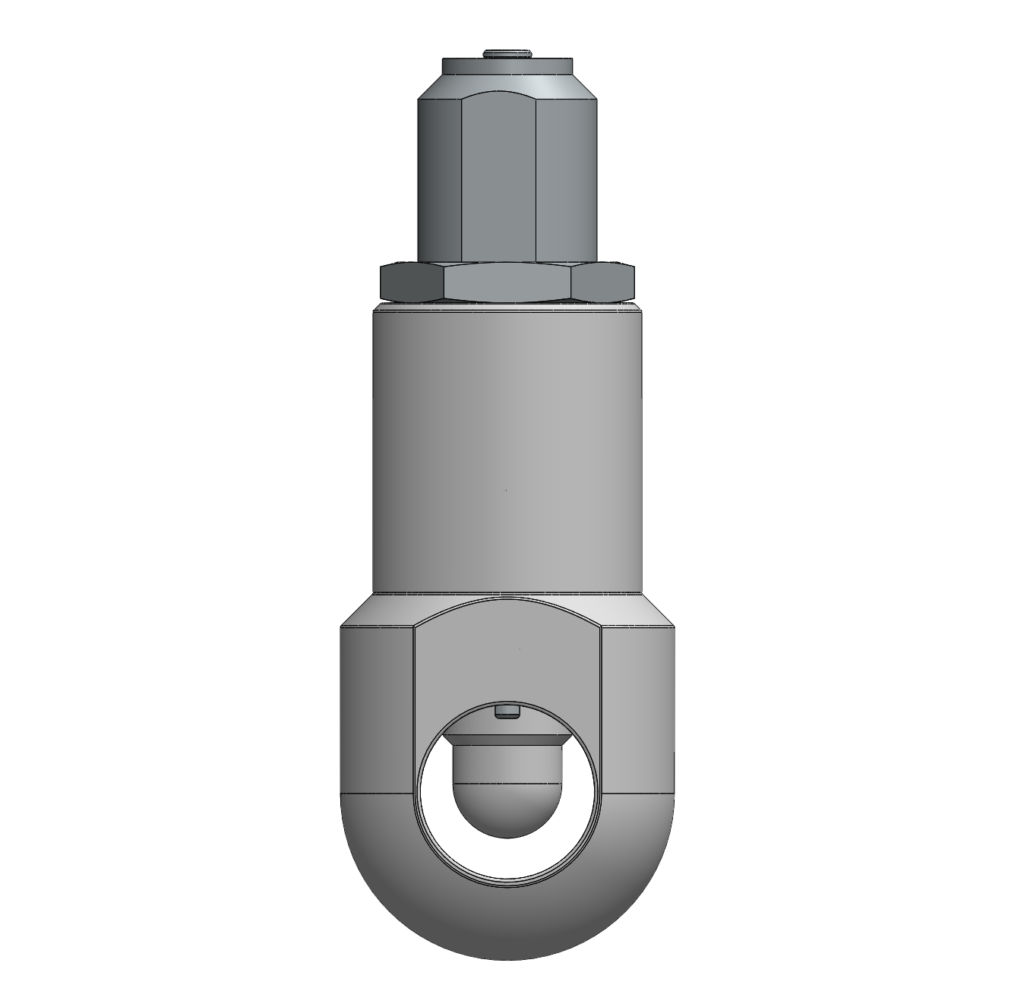
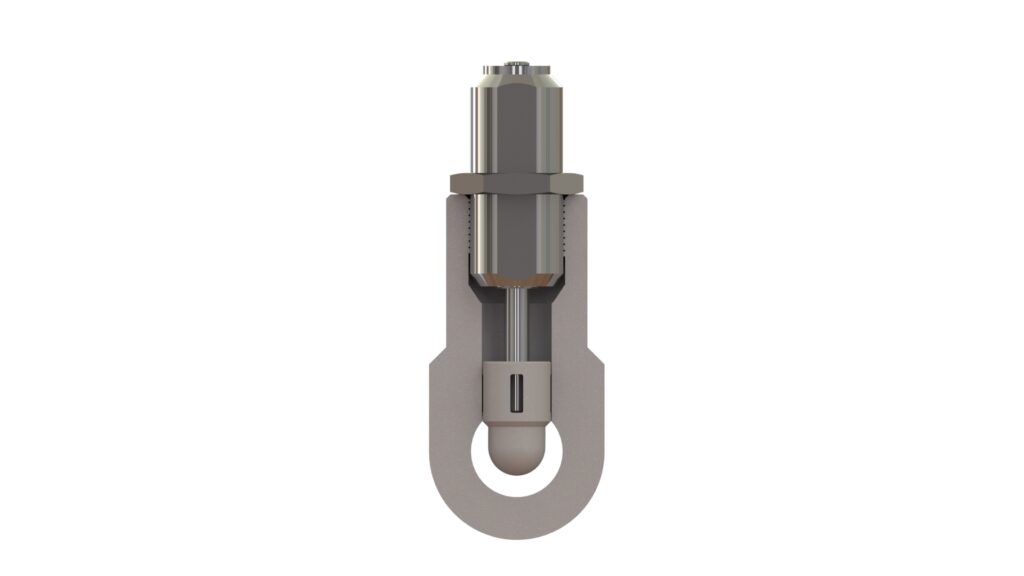
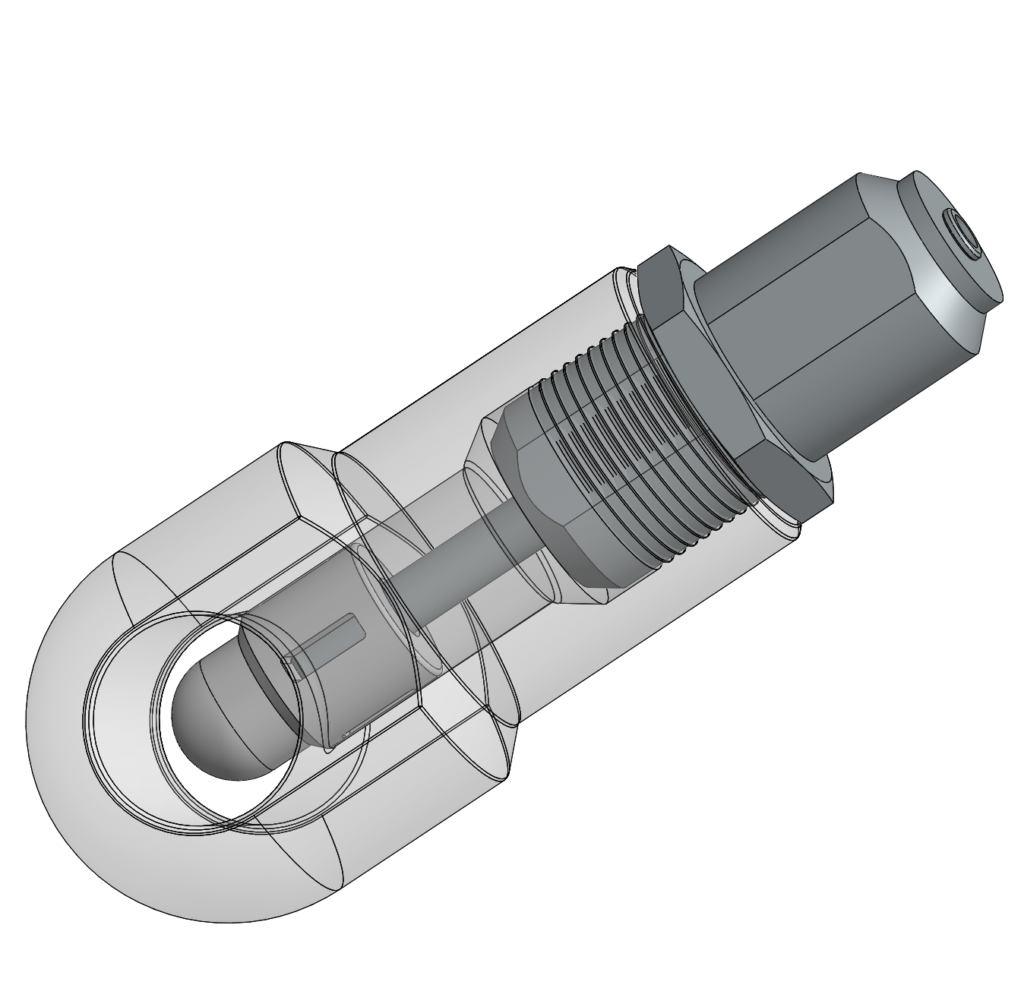
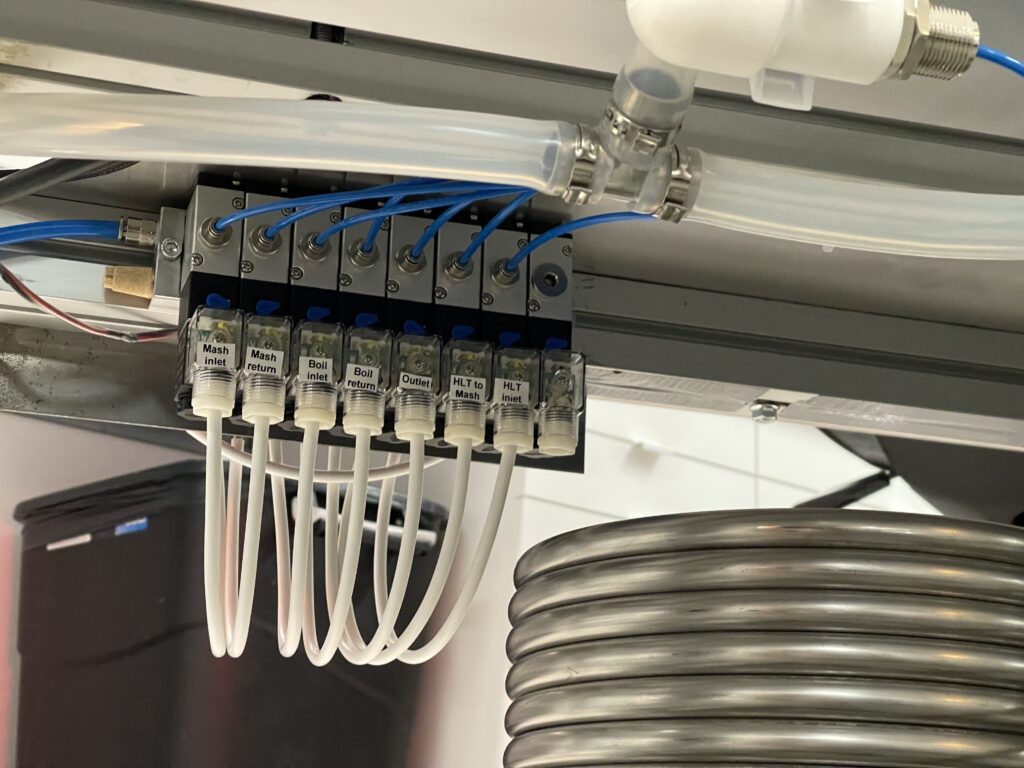
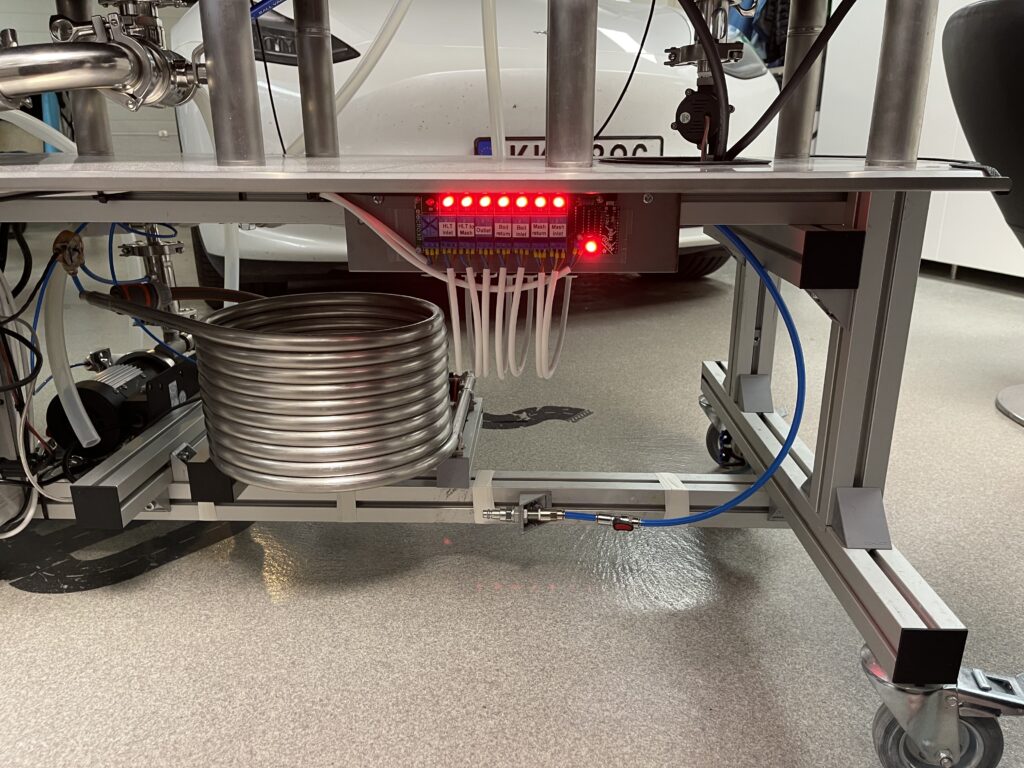
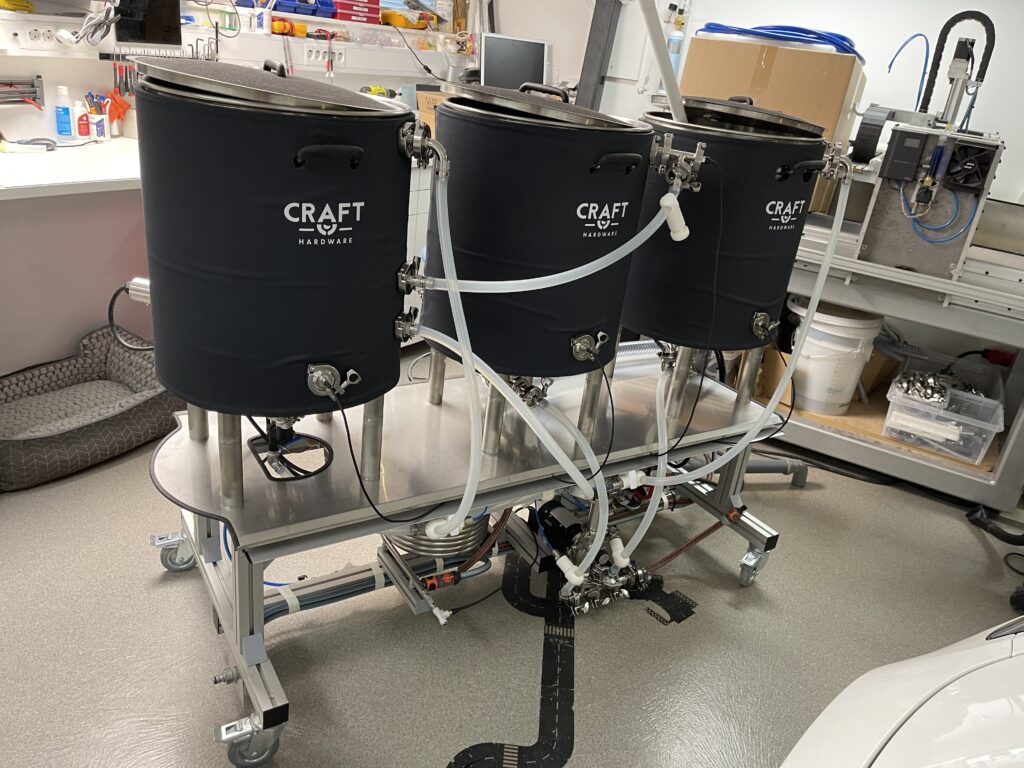
The position of the valves is controlled by an array of 8 solenoid valves from Amazon and an 8x relay board with a small Arduino placed between the brewery’s Raspberry Pi and the relay board, which is controlled via USB since we don’t have enough GPIOs to control the valves directly from the RPi. The relay board is configured so that during startup and in case the 5V power supply is lost, the pinch valves will remain closed to avoid the risk of them opening in the event of a system failure.
The drawback of these valves is their reliance on compressed air, but if you have access to it, it’s not a significant issue.
A positive outcome of increasing the hose dimensions and shortening the flow paths was that the maximum flow rate increased by more than a factor of 2, going from around 10 L/minute to over 20 L/minute. Another beneficial effect was that we could ensure that all hoses were inclined towards a common lowest point to facilitate drainage after cleaning.
BOM
STL-files, other formats on demand
Pin cylinder: Camozzi 14N1A16A15
Designed for silicone hose with YD 21 mm, ID 15 mm