Knowing the “exact” wort volume in a fermenter is “crucial” for quality control during the brewing process. However, measuring the volume accurately and continuously can be a challenge. At our brewery, we use differential pressure sensors for various measurement tasks, and we realized that this technology could also be used to estimate the wort volume in our fermenter.
To achieve this, we installed a differential pressure sensor between the bottom of the cylindrical part of the fermenter and the top of the fermenter. By measuring the differential pressure between these two points, we can calculate the weight of the wort above the bottom reference point. Knowing the volume below the reference point (a constant), the specific gravity of the wort, and the diameter of the cylindrical part, we can calculate the wort volume.
However, one problem we encountered was that the gas in the fine pipe used to measure the bottom reference point could be compressed by the increasing absolute pressure in the fermenter, resulting in inaccurate volume estimates. Additionally, CO2 in the pipe could dissolve into the wort, causing further measurement errors. To address this, we developed a closed system that uses the existing gas (primarily CO2) in the fermenter headroom to flush the pipe.
Our closed system involves two valves and a syringe to extract gas from the headroom and push the gas back through the pipe. This system allows us to flush any liquid out of the pipe and ensure that it only contains gas for accurate volume estimates.
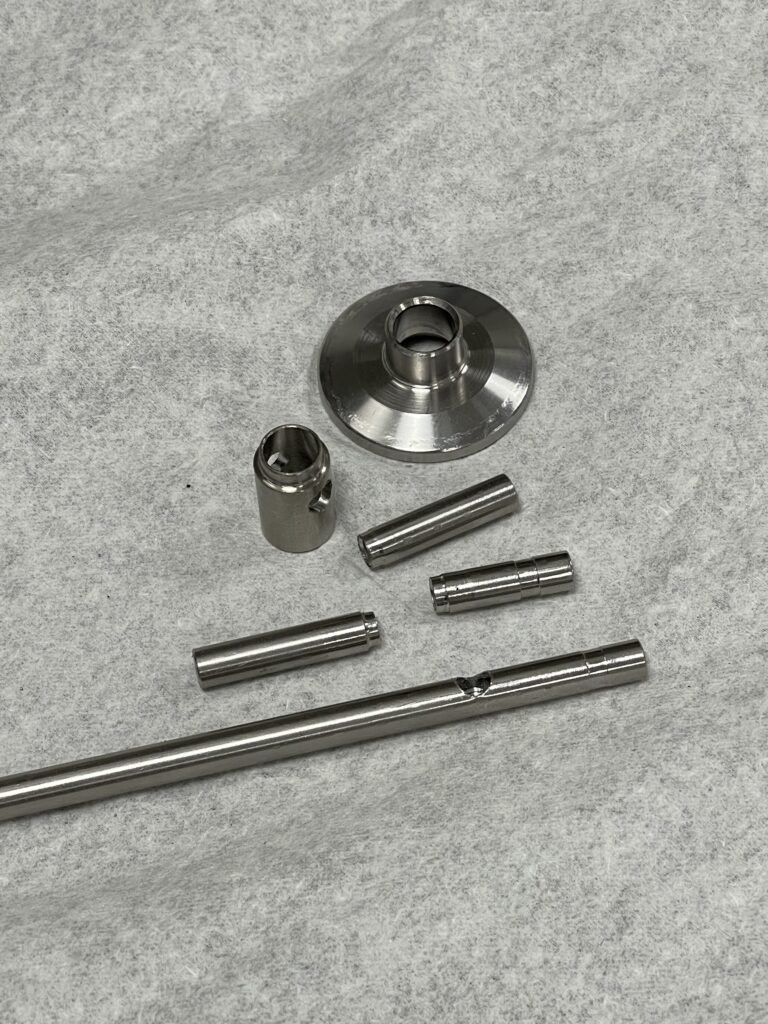
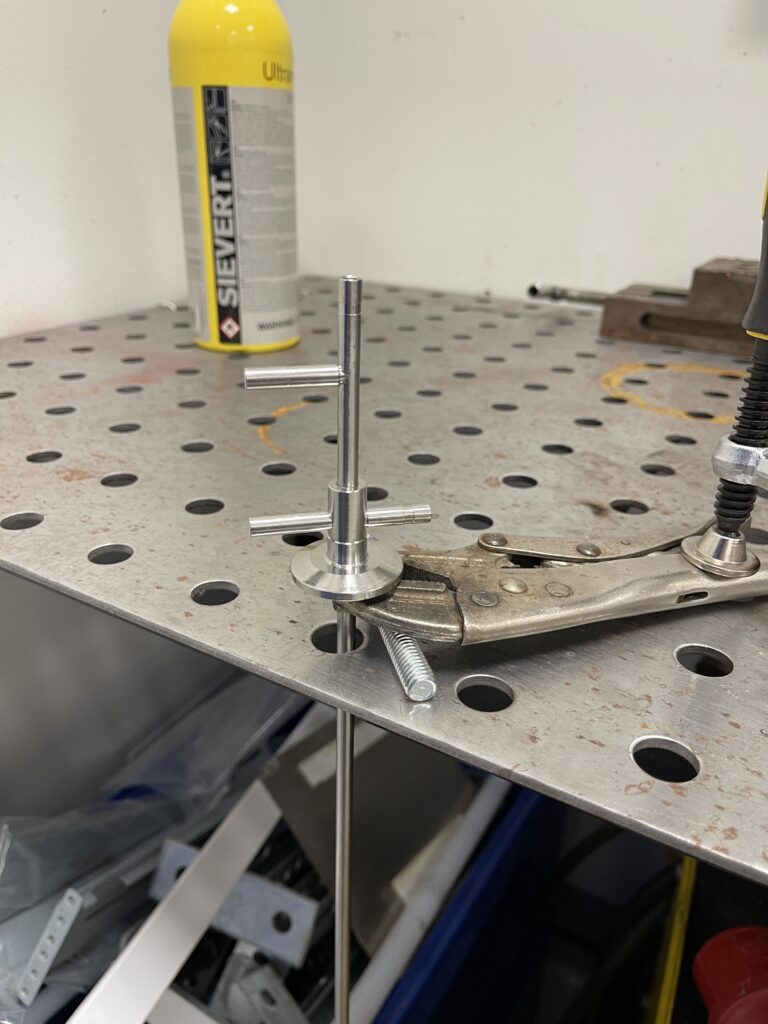
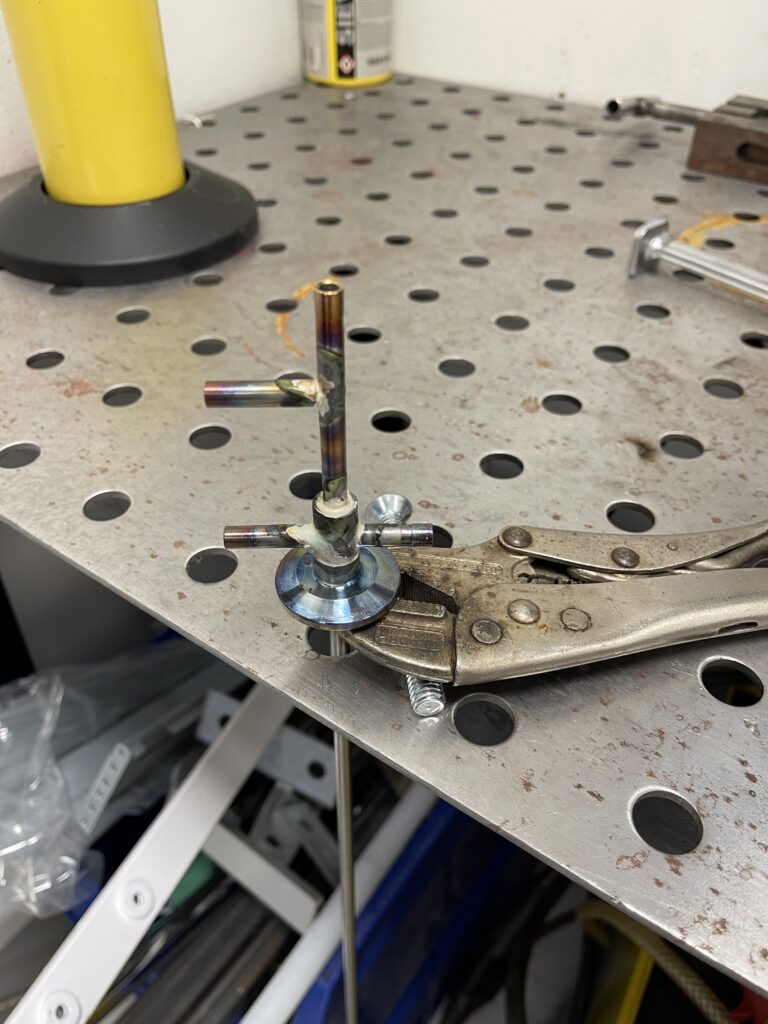
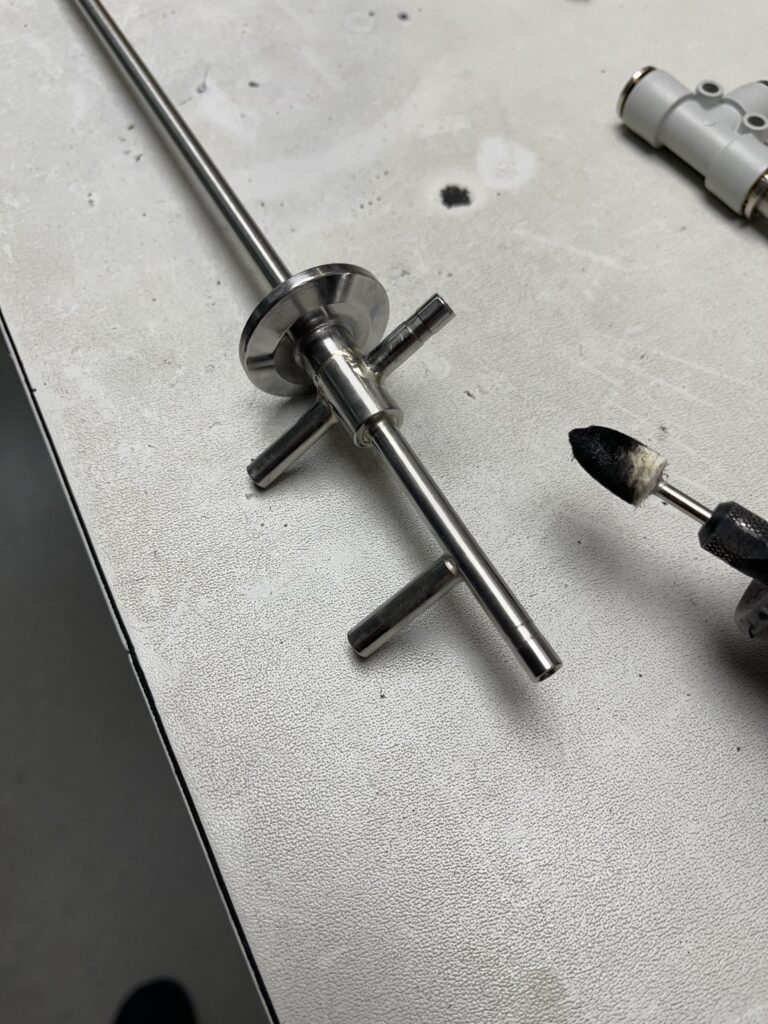
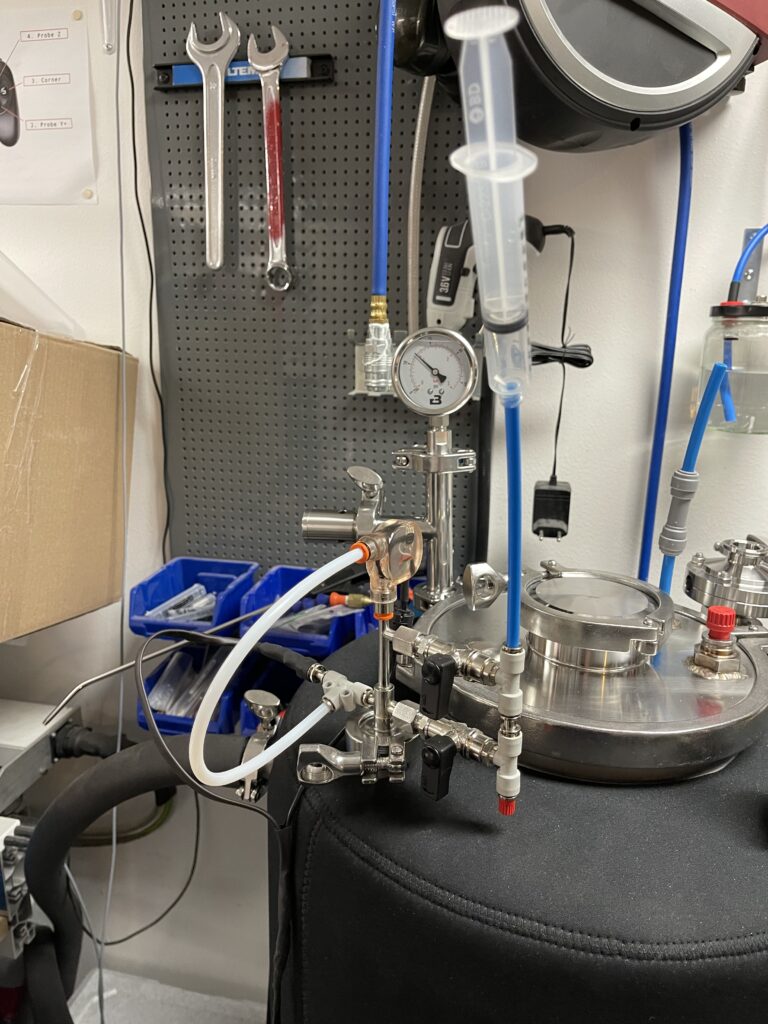
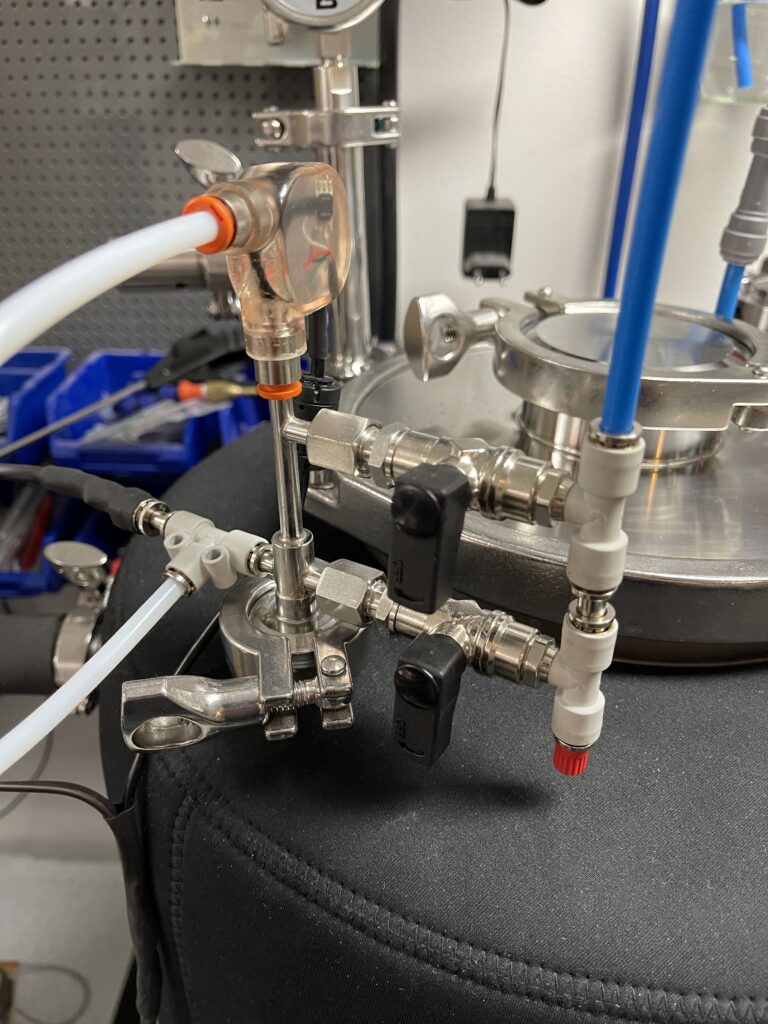
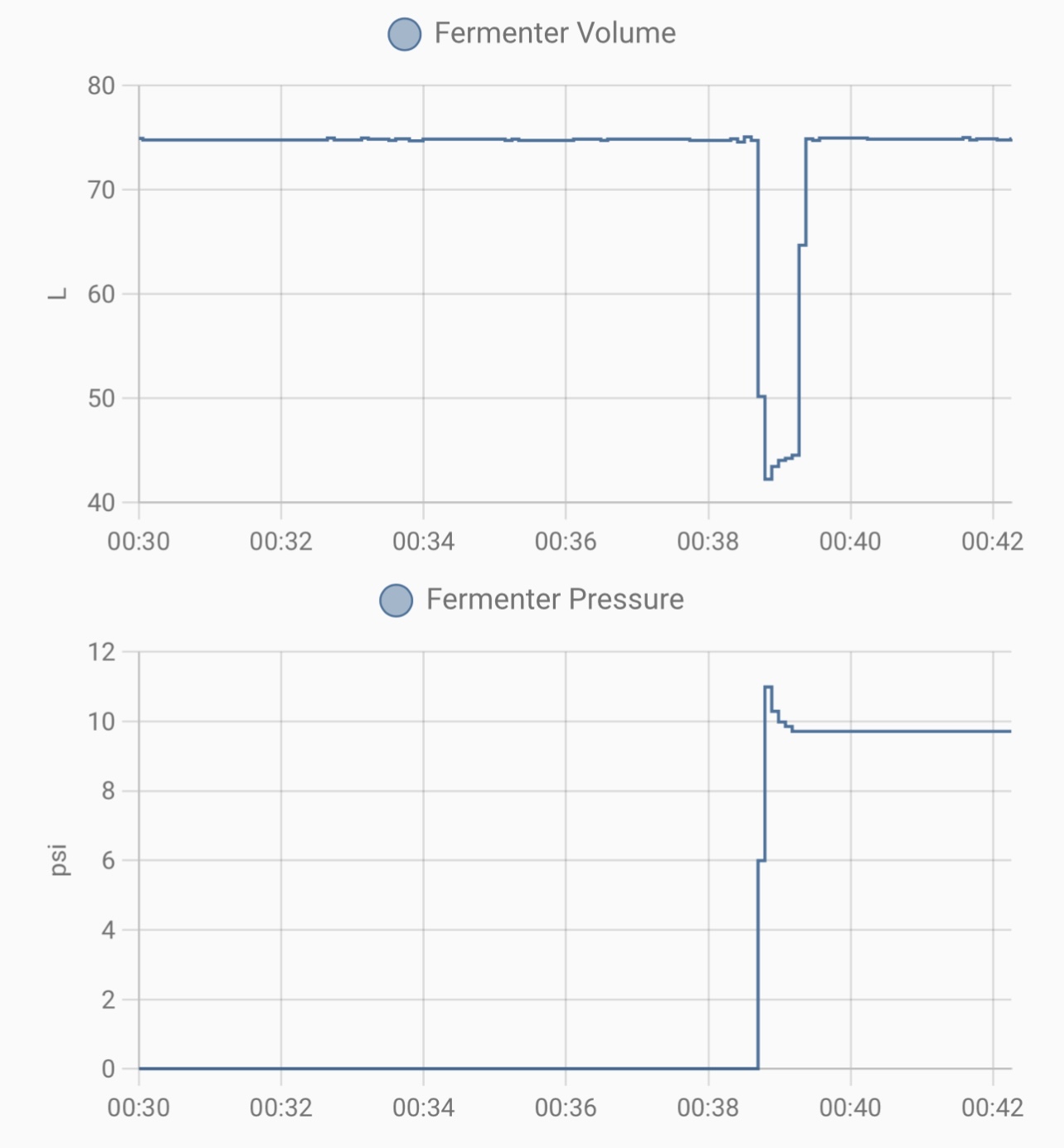
The sensor measures 75L (with 75 kg of clean water in it) at normal air pressure. When we put the fermenter under 10 PSI of pressure (air, not CO2), the measured volume goes down due to the gas in the pipe being compressed. However, after purging the pipe, the volume returns to 75L again.
At the time of writing, the volume sensor system has not been tested with wort and real fermentation conditions, including a wide range of temperatures, pressures, densities, and so on. We are excited to test this system further and believe it has great potential.
To be continued!